JT Group Monitoring Indicators on Health and Safety
Health and Safety
The JT Group recognizes that achieving JT Group Purpose requires work environments that actively promote health, safety, and wellbeing for employees, contractors, and visitors alike. By supporting individuals physically and mentally, we aim to create the conditions where everyone can fully apply their capabilities and engage meaningfully in their work.
That is why we uphold the philosophy of "People come first," placing the utmost importance on safety and health and aim for zero harm that is zero work-related physical injury or mental damage in the JT Group Health and Safety Policy. We put a range of measures in place, such as raising employee safety awareness under this policy.
JT Group Health and Safety Policy
To further promote health and assure safety at work, the JT Group has established the JT Group Health and Safety Policy approved by the Board of Directors.
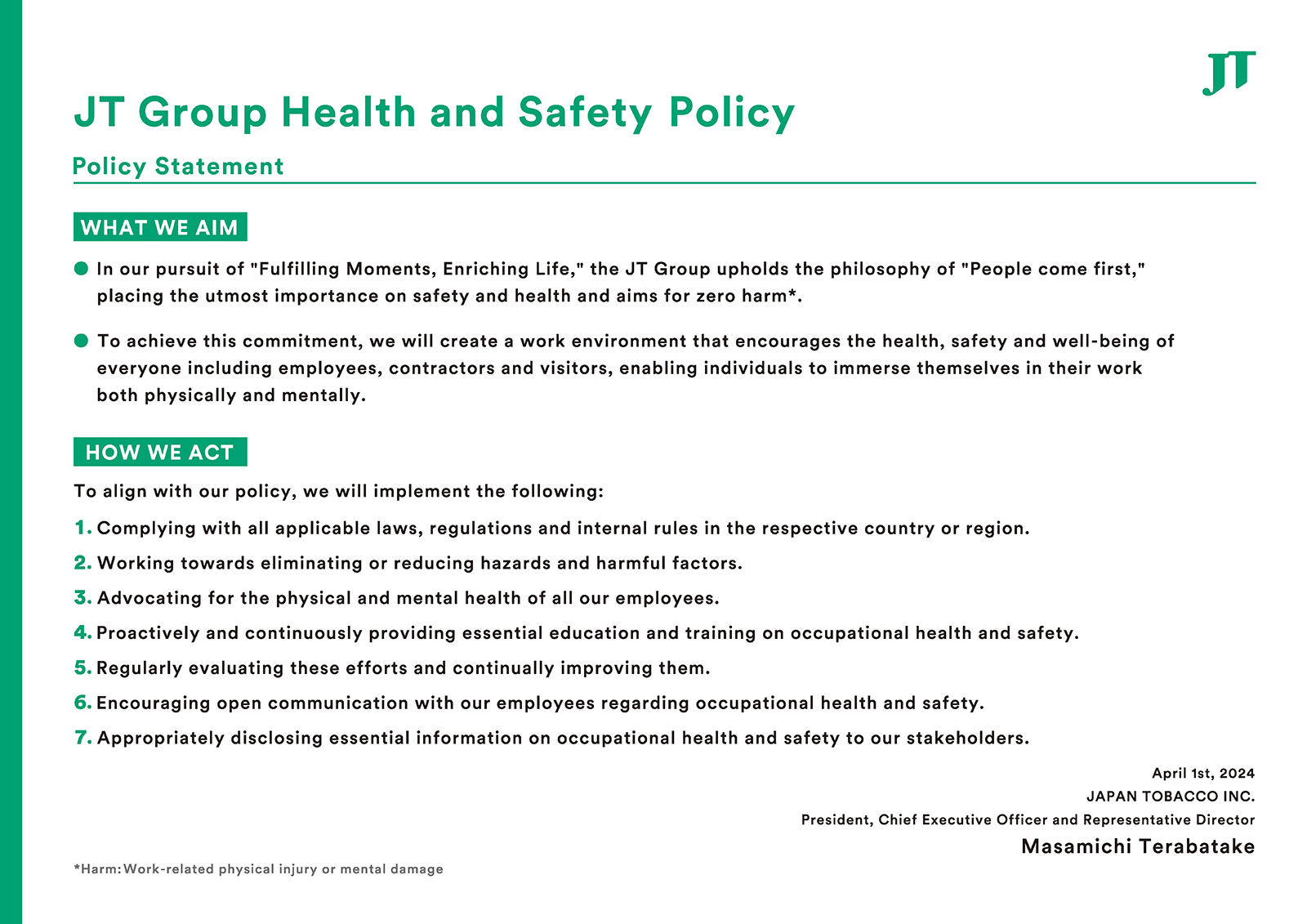
Health and Safety System
We implement health and safety initiatives under the responsibility of the JT CEO and enhance group governance under a system supervised by the Board of Directors.
Each business within the JT Group must maintain a Health and Safety Policy aligned with the Group’s Policy. These policies must be committed to preventing injuries and illnesses, complying with legal requirements, involving workers in safety matters, and driving continuous improvement. They must address key risks, outline prioritized action plans, be reviewed regularly, communicate to all employees and contractors, and make available to relevant stakeholders.
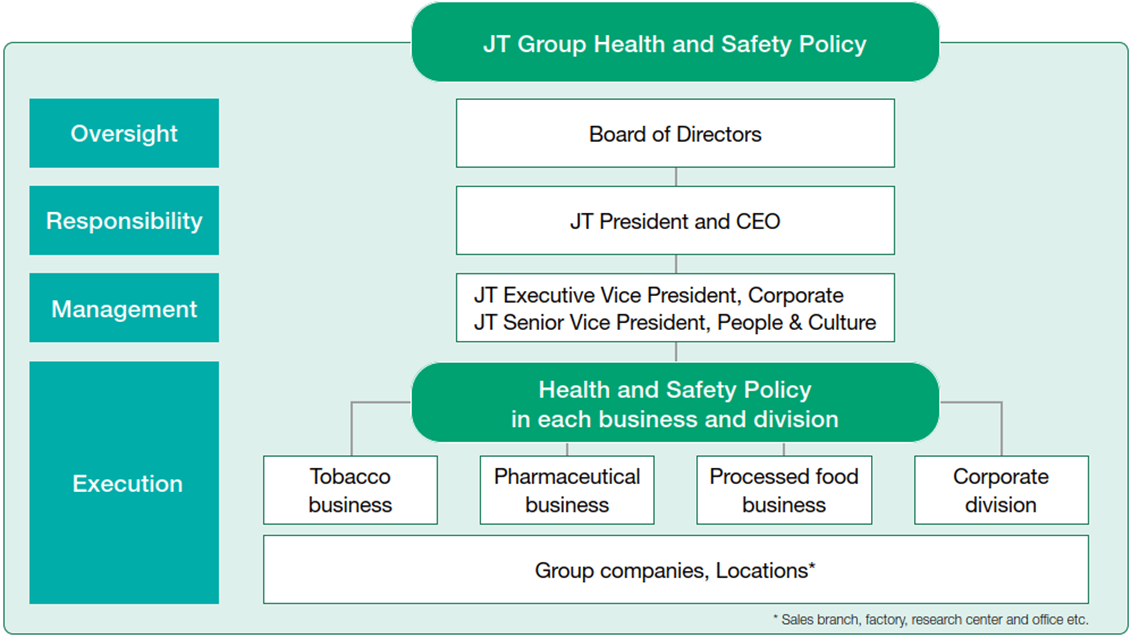
- * While on May 7th, 2025, the Company announced entering into an agreement with Shionogi & Co., Ltd. to transfer the pharmaceutical business and our stake in TORII PHARMACEUTICAL CO., LTD. ("Torii"), a consolidated subsidiary of JT, the JT Group's performance and initiatives described on this page include those associated with the pharmaceutical business and Torii. Please see the press releases on our website for the details.
- As announced on September 1, 2025, the transfer of Torii shares has been completed. Please see the press release on our website for the details.
Health and Safety Initiatives
The JT Group has processes for identifying and minimizing risks, preventing incidents, responding to emergency situations, and continuously improving safety.
We are committed to achieving zero work accidents by implementing preventive measures tailored to the specific risks of each operation. Risk assessments have identified driving vehicles and machinery operation as high-risk activities. In response, we are focusing on raising employee awareness and enhancing work environments to reduce these risks and promote safer practices.
At overseas locations in the tobacco business with driving vehicles, we are introducing an app that analyzes driver behavior and provides tailored individual advice. The app is currently being used by around 3,000 drivers. We also hold safe driving trainings for drivers who have a high risk of causing accidents. In addition, we have introduced guidelines aimed at preventing accidents involving pedestrians to increase driver safety awareness and risk management capabilities, while fostering a safety culture.
On locations with machinery operation, we are involved in the formulation of targets and plans, the identification of risks through hazard prediction activities, the implementation of measures to reduce risks such as modifying machinery, and the evaluation and auditing of these initiatives.
Among these, in the tobacco business we have created procedure manuals for safe operations during machine operation and maintenance, and roll out globally. We also collaborate with machinery manufacturers to improve the design and safety standards of machinery. Moreover, in addition to complying with local laws and regulations, we are working to obtain ISO 45001 certification, the international standard for occupational health and safety management systems, on a global basis. Approximately 70% of tobacco factories have obtained this certification.
The TableMark group in our processed food business has been conducting group-wide initiatives under the Zero Work Accident Project, with members from across multiple companies and divisions.
In the case of work accidents related to driving vehicles, for example, the group collects examples of initiatives for preventing traffic accidents at sales offices throughout Japan and distributes videos aimed at raising safety awareness. In addition, each group company and location have put in place checking systems to ensure compliance with laws and regulations, such as alcohol checks and license expiry date checks.
To address work accidents involving operating machines, the group is working to enhance education on safe operation including on-the-job training and to implement factory inspections by other manufacturing sites and external experts. It is also trying to strengthen connections between manufacturing sites by sharing the result of risk assessments and establishing unified rules.
The JT Group is implementing health and safety education and training at every company and location, aiming to foster safety awareness and a safety culture, as well as to improve employees’ knowledge and skills related to health and safety.
<Main Health and Safety Education and Training for FY2024>
Topic | Content |
---|---|
Risk assessment |
・ Hazard prediction activities ・ Seminar for upskilling on causal analysis and measure planning for work accidents ・ Session for sharing causes and preventative measures in work accident cases related to machinery operation |
Driving vehicle |
・ Safe driving seminar (preventing drink-driving, responsibility and impacts of traffic accidents) ・ Seminar on preventing accidents caused by poor visibility ・ On-road training |
Emergency response |
・ Training on operation of fire hydrants and fire alarm equipment ・ Earthquake simulation training using VR equipment ・ Training on use and cautionary points regarding AEDs, and CPR |
As a result of these initiatives, in the FY2024 JT Group Employee Engagement Survey, over 80% of employees responded “I feel appropriate measures are taken at my workplace to prevent injuries and illnesses”.
For information on JTI initiatives, please refer to here.
Monitoring Indicators
Based on the JT Group Health and Safety Policy we have set up monitoring indicators to track the JT Group health and safety initiatives, and institute measures promptly as they are determined as necessary.
In addition, the Board of Directors supervises JT Group Health and Safety System based on the result of performance related to health and safety with a focus on this monitoring indicators reported at least once a year.
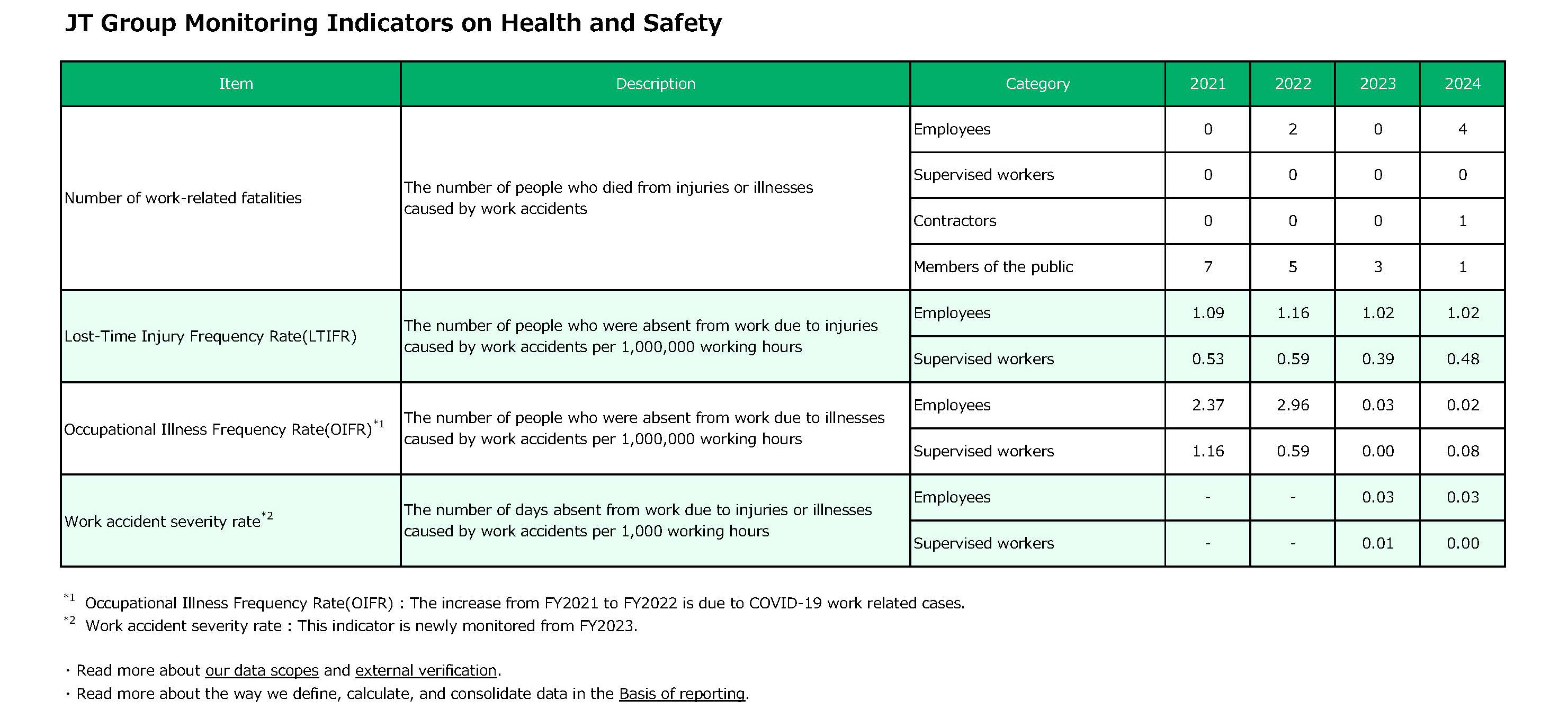
For serious work accidents that involve fatalities and so forth, we rigorously implement recurrence prevention to ensure that the same accident does not occur again.
For example, when a serious traffic accident, we conducted a comprehensive analysis of the condition of the driver, such as vehicle speed and driving experience, the condition of the road, including visibility and road surface, and vehicle maintenance condition. We then conducted training for inexperienced drivers with a focus on driving skills for unpaved roads, and introduced real-time alerts for excessive speed using telematics, and the Behavior Observation System which employees monitor and raise awareness each other regarding unsafe driving. We are sharing this approach globally to connect it to risk assessment in countries where the same kind of work accident could occur.
Furthermore, we have a system that enables rapid reporting of the occurrence of serious work accidents and recurrence prevention measures to our Directors, as well as the receipt of feedback as needed.
Looking ahead, we will carefully monitor the status of work accident occurrences in the JT Group, and continuously promote effective measures toward the achievement of zero work accidents.